Our ability to store energy in ‘Batteries’ is of global environmental importance as we move away from the instant energy of burning fossil fuels. If we could store all the energy renewables produce then we’d get to the global net zero targets already so Batteries literally have the potential to save the planet.
Is Lithium-Ion still the right technology for consumer electronics, home energy or EVs though? Can we produce enough for the future when the raw materials are scarce now? Which of the numerous alternatives are future proof? And while negotiating this technology innovation during geo-political turbulence, who should you trust your manufacturing and logistical supply chains to?
The alternatives to lithium-ion are numerous but the path forward is far from clear. British firm Faradion is developing a sodium-ion battery, replacing lithium with the cheaper and more readily available sodium, but they may not make the leap to electronics for EVs due to limitations in energy density and recharge life. Universities in Japan have made significant advances on solid-state batteries to replace the liquid electrolytes. Tokyo University of Science professor Shinichi Komaba believes sodium-ion batteries can be commercialised but may not replace lithium-ion batteries however controversially the MIT Technology Review mentioned Chinese battery giant CATL’s plans to begin mass-producing sodium-ion batteries in 2023. Meanwhile others are considering lithium-air and lithium sulphur batteries for electric vehicles.
With so much global scientific innovation in batteries it is clear that truly collaborative technical and logistical partnerships are critical to make the right choices.
If Lithium-ion remains the key technology in mass manufacturing mechatronics there is one critical consideration though – safety. Lithium-ion cell and battery manufacturing assembly processes require stringent quality control because improper design and manufacturing practices can lead to catastrophic failures here and later during product use.
Samsung’s infamous battery ‘instances’ were unusual, but they’re not the first products to catch fire or be recalled. Lithium-ion batteries power laptops, cellphones, and cameras, despite their hazard. Will we see electronics manufacturers releasing products with less efficient, more costly, but safer batteries in 2023?
Our robust and highly automated processes include the Battery Management System that has proved critical to minimizing these risks. BMS is the control system within the battery pack that consists of one or more electronic controllers managing the charging/discharging; it monitors the temperature/voltage, communicates with the product system, balances the cells, and manages the safety functionality of the battery pack.
It is because Battery safety is so critical that our record of zero-safety recall record on 35 million battery packs shipped means Microtronics has earned its leading partner credentials.
The Manufacturing teams at Microtronics thrive on tackling ever-increasing complexity at the required scale for any global electronics partner. Our tooling and manufacturing operatives, logistics experts and supply chain managers are the match of our manufacturing expertise – our fully automated tungsten electrode welding for instance delivers superior welding quality with error proofed safety checks and quality controls as part of the process.
Our advice in these times of great innovation and environmental significance is to choose a battery pack manufacturing and logistics partner whose record of safety is impeccable because with the technology developing so fast, mistakes are more likely. Cost is not the only issue. Trust is critical.
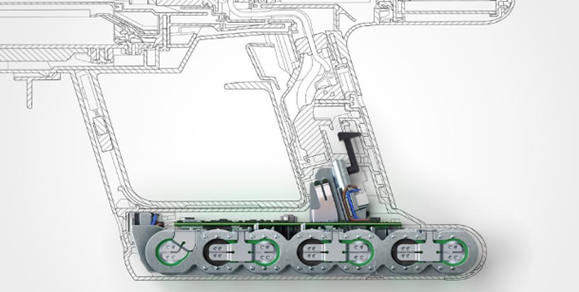
About the Author: Mosses Antony, Group Director
Mr. Mosses Antony has approximately 25 years of diversified and extensive expertise leading end-to-end manufacturing operation, quality, and R&D. He worked together with international scientists and university academics on battery solutions. He ran Microtronics’ precision battery pack assembly lines for 4 years. Innovative and adaptable organisational leader focused on ESG efforts.
References:
Warner, J. (2015). The handbook of lithium-ion battery pack design: chemistry, components, types and terminology. Elsevier Inc.
Kobie, N. (2016, Sep 14). Samsung battery recall: Why lithium-ion batteries catch fire. IT Pro, Retrieved from http://ezproxy.bac.edu.my:2048/login?url=https://www-proquest-com.ezproxy.bac.edu.my/magazines/samsung-battery-recall-why-lithium-ion-batteries/docview/1819245200/se-2
https://www.dyson.co.uk/support/vacuum-cleaners/cordless/battery-care
Carter, S. (July 26, 2012). Nissan pens open letter to LEAF customers affected by battery capacity loss. Nissan LEAF Electric Car News. Retrieved August 3, 2014, from http://nissan-leaf.net/2012/07/26/nissan-pens-open-letter-toleaf-customers-affected-by-battery-capacity-loss/
Battery Management System (no date) Battery Management System – an overview |ScienceDirect Topics. Available at: https://www.sciencedirect.com/topics/chemistry/battery-management-system (Accessed: February 19, 2023).